石墨模具加工在现代工业中扮演着至关重要的角色,尤其是在汽车制造、机械加工、航空航天等领域。为了确保石墨模具的高精度和优质表面,优化工艺设计显得尤为重要。
石墨材料的选择
选择合适的石墨材料是确保石墨模具加工精度的第一步。石墨材料应具备高纯度、细密度、低气孔率、低热膨胀系数等特点,以确保模具的稳定性和精度。常见的石墨材料有高密度石墨、超细晶石墨、等向石墨等,根据具体加工要求选择合适的材料。
精密加工设备的运用
精密加工设备是确保石墨模具加工高精度的关键。高精度的加工设备可以提供更稳定的工作环境和更高的加工精度。常见的精密加工设备包括高速数控铣床、电火花机床、激光切割机等,使用这些设备可以满足对模具尺寸精度、表面质量等要求。
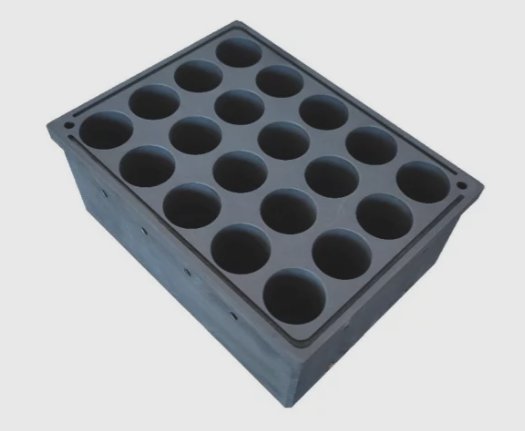
数控机床的选择与操作
数控机床的引入为石墨模具加工带来了巨大的改进。数控机床需要具备高精度的定位和运动控制系统,以确保加工过程中的位置和运动的稳定性。同时,数控机床应该配备先进的冷却系统,有效降低切削温度,提高加工精度。
合理的工艺设计与优化
合理的工艺设计与优化是实现高精度加工的关键环节。在设计加工工艺时,应综合考虑石墨材料的特点、加工设备的性能以及实际加工要求,合理选择切削参数、工艺路线等。同时,还需要进行工艺优化,通过试刀、试模等方式不断改进工艺,提高模具加工的精度和效率。
刀具选择和切削参数调节
刀具的选择和切削参数的调节对石墨模具加工的精度具有重要影响。选择合适的刀具材料和设计刀具几何形状,能够有效减少切削力,提高加工精度。同时,根据石墨材料的特性,合理调节切削参数,如切削速度、进给速度和切削深度,以获得最佳的加工效果。
工艺设计和加工路径优化
合理的工艺设计和优化的加工路径也是确保高精度的关键。工艺设计应考虑石墨材料的热膨胀系数和热导率等特性,合理控制加工温度和热变形。同时,通过优化加工路径,减少刀具的快速移动和频繁停留,减少振动和切削力的影响,提高加工精度。
表面处理和质量检测
表面处理和质量检测是确保石墨模具加工高精度的最后环节。通过有效的表面处理方法,如抛光或镀膜,能够改善石墨模具的表面光洁度和耐磨性,提高模具的使用寿命和加工精度。同时,采用精密的质量检测方法,如三坐标测量仪或投影仪,对加工后的石墨模具进行全面的尺寸和形状检测,确保达到设计要求。
常用检测方法
常用的检测方法包括三坐标测量、光学显微镜观察、表面粗糙度测试等。通过这些检测手段,可以及时发现加工中存在的问题,并采取相应的措施进行修复和调整。